Encapsulation of Electronic Components
Glob Top and Frame & Fill encapsulation provides protection for individual electronic components attached to PCB’s and FPC’s. Encapsulated components, like flip-chips, semiconductor die chips, delicate lead wires, etc., are shielded from environmental stresses, contamination, and mechanical vibration. Encapsulating materials serve to neutralize dissimilar Coefficient of Thermal Expansion (CTE) values between the component and board. In addition, these materials improve individual component insulation, minimizing current loss.
Glob Top and Frame & Fill processes are integrated into automated assembly lines using programmable, robotic dispensing equipment. The encapsulating materials are deposited directly on the components and boards in precise, repeatable patterns.
Panacol-USA produces single component, light curable encapsulants with performance properties that are ideal for high volume production lines. These encapsulation materials are highly resistant to contaminants, cure with minimal shrinkage, and remain extremely flexible to minimize risk of damage to fine wire leads and connections.
Similar to sealants and coatings, encapsulants provide environmental protection for individual electronic components such as diodes, capacitors, and integrated circuits (IC), as well as wire leads and other fragile connectors. The encapsulant’s composition must reflect high ionic purity, and preferred cured properties include moisture resistance, invulnerability to thermocycling, low shrink, and flexibility from a low modulus value. Low shrink and flexibility are significant as the encapsulant also functions as a strain relief for fine wire leads. Lower stress minimizes the risk of wire breakage.
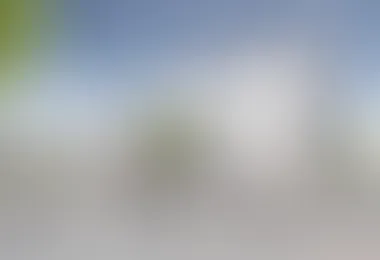
Black glob top adhesives are applied on smart card chips to protect the chips from damage
UV curing equipment:
UV system solutions with Panacol uv curable adhesives and innovative curing systems from Honle
Download brochure:
Encapsulants offered by Panacol-USA have been formulated with all these desirable properties in mind. Panacol-USA’s line of encapsulants feature excellent adhesion to substrates associated with PCB and FPC assembly, including polyimide, metals, FR-4 (glass-epoxy), PET, polycarbonate, ceramic, and glass. They are offered in a range of viscosities to better support numerous component geometries. For example, in order for the encapsulant to create a uniform coating (shell) on sharp-edged components, it should generally be higher in viscosity and thixotropic.
View the Encapsulant products listed below for a possible candidate for your application. Please contact Panacol-USA to confirm your product selection and to secure additional application assistance, including samples and process recommendations. In the event that these standard products do not satisfactorily address your performance requirements, Panacol-USA will investigate other solutions that include development of adhesive specifically tailored to the complexity of your application.
New from Panacol are single component epoxy adhesives that cure at low temperatures, (60oC). Structalit® 5511, 5521, and 5531 adhesives were specifically formulated for microelectronics applications and adhere very well to low surface energy substrates. These products are ideally suited for encapsulating temperature sensitive components on PC boards. Find them in our table below and click on their Technical Data Sheets for more detailed information.
Encapsulant | Viscosity [mPas] | Base | Curing* | Properties |
---|---|---|---|---|
Structalit® 5800 | 7,000-15,000 mix (LVT, 25°C, Sp. 4/30 rpm) | 2-part epoxy | thermal, room temperature |
High temperature resistance short pot life fast application |
Structalit® 5810-1 | 3,000-4,000 mix (LVT, 25°C, Sp. 4/30 rpm) | 2-part epoxy |
thermal room temperature |
Very high adhesion to PC resistant to moisture and chemicals |
Structalit® 5891 | 25,000-50,000 ( Rheometer, 25 °C, 10s-1 ) | epoxy | thermal |
Black color fast curing at low temperatures impact resistant |
Structalit® 5891 T | 80,000-150,000 (Rheometer, 25 °C, 10s^-1 ) | epoxy | thermal |
Black color stable frame material, can be applied wet-in-wet with filling material, suitable for frame stacking stable edges resistant to shocks |
Structalit® 5893 | 6,000-10,000 (Rheometer, 25°C, 10s^-1) | epoxy | thermal |
Black color excellent flow properties filling material for frame&fill applications high resistance to heat and chemicals certified to ISO 10993-5 standards |
Structalit® 5894 M | 20,000-30,000 (Rheometer, 25 °C, 20s ^-1) | epoxy | thermal |
Black color excellent flow properties filling material for frame and fill applications on PCBs, very high resistance to heat and chemicals |
Structalit® 8801 | 30,000-45,000 (LVT, 25°C, Sp. 4/6 rpm) | epoxy | thermal |
Resistant to oils, grease and fuels excellent flow properties beige color certified to ISO 10993-5 standards |
Structalit® 8805 | 30,000-45,000 | epoxy | thermal |
Resistant to oils, grease and fuels excellent flow properties beige color |
Structalit® 8838 | 6,500-7,500 (Rheometer, 25°C, 20s^-1) | epoxy | thermal |
Black color flexible potting compound excellent flow properties |
Vitralit® 1600 LV | 3,000-5,000 | epoxy |
UV secondary heat cure |
Very high Tg low water absorption low ion content very high chemical resistance |
Vitralit® 1605 | 200-400 (LVT, 25°C, Sp. 2/30 rpm) | epoxy |
UV secondary heat cure |
low shrinkage low heat expansion very high tg excellent chemical resistance certified to ISO 10993-5 standards |
Vitralit® 1655 | 150-300 (Brookfield LVT, 25 °C, Sp. 2/30 rpm) | epoxy |
UV secondary heat cure |
flexible certified to USP Class VI and ISO 10993-5 standards resistant to all common sterilization methods |
Vitralit® 1671 | 9,000-14,000 (Rheometer, 10s^-1) | epoxy |
UV secondary heat cure |
Stable frame compound high ion purity electronic grade adhesive high temperature conductivity low water absorption UL94 HB test passed |
Vitralit® 1688 | 1,200-2,000 | epoxy | UV |
Excellent flow properties and leveling electronic grade adhesive low ion content suitable for chip protection excellent resistance to heat and humidity |
Vitralit® 1691 | 20,000-40,000 | epoxy |
UV secondary heat cure |
black color high ion purity electronic grade adhesive high temperature resistance fast surface curing with UV light |
Vitralit® 1722 | 5,000-8,000 (LVT, 25 °C, Sp. 4/30 rpm) | epoxy | UV |
Very high adhesion to most thermoplastics low shrinkage high temperature resistance |
Vitralit® 5140 | 250-500 | acrylate |
UV VIS |
Flexible, well suited for bonding plastics with low UV translucence and permeable to visible light, biocompatible: certified to USP Class VI standards |
Vitralit® 6103 | 3,500-5,000 | acrylate |
UV secondary heat cure |
Very high adhesion to metals and sintered materials transparent |
Vitralit® 6104 | 3,000-8,000 | acrylate |
UV secondary heat cure |
Very high adhesion to metals and sintered materials |
Vitralit® 6104 VT | 8,000-17,000 (Rheometer, 25°C, 10s^-1) | acrylate |
UV secondary heat cure |
Very high adhesion to metals and sintered materials ideal for bonding large components on circuit boards (corner bonding) |
Vitralit® 6105 | 3,500-6,000 | acrylate |
UV secondary heat cure |
very high adhesion to metals and sintered materials |
Vitralit® 6125 | 4,000-6,000 (LVT 25°C, Sp. 4/30 rpm) | acrylate |
UV secondary heat cure |
excellent adhesion to stone, glass, metals and thermoplastics medium viscosity |
Vitralit® 6128 | 800-1,200 | acrylate |
UV secondary heat cure |
very high adhesion to stone, glass, metals and thermoplastics high temperature resistance |
Vitralit® 6128 VT | 3,000-6,000 (Rheometer, 25°C, 10s^-1) | acrylate |
UV secondary heat cure |
contains chemical activator high temperature resistance high viscosity excellent adhesion to stone, glass, metals and thermoplastics |
Vitralit® 9180 | 700-1,200 | acrylate | UV |
Dry surface fast curing of thick layers yellow color |
Vitralit® 9181 | 4,000-7,000 | acrylate | UV |
Yellow color dry surface fast curing of thick layers |
Vitralit® UD 5180 | 4,000-6,000 | epoxy |
UV secondary heat cure |
Perfect solution for bonding flexible circuit paths resistant to reflow processes grey color |
Vitralit® VBB-1 | 1,000-1,500 | acrylate |
UV VIS |
Elastic high peel strength optically clear very flexible suitable for potting |
Vitralit® 2004 F | 60-100 (LVT, 25 °C, Sp. 2/30 rpm) | epoxy |
UV secondary heat cure |
fluorescing flexible autoclavable dry surface after curing low ion content sprayable |
Vitralit® 2007 F | 150-350 (LVT, 25 °C, Sp. 2/30 rpm) | epoxy |
UV secondary heat cure |
fluorescing flexible autoclavable excellent chemical resistance low ion content |
Vitralit® 2009 F | 100-200 | epoxy |
UV secondary heat cure |
fluorescing flexible autoclavable high chemical resistance low ion content |
Vitralit® 2028 | 160-300 | epoxy |
UV secondary heat cure |
Dry surface after UV-curing autoclavable excellent chemical resistance scratch resistant coating |
Vitralit® 4451 MV F | 2,000-3,000 (LVT, 25 °C, Sp. 4/30 rpm) | acrylate | UV, VIS |
soft and elastic dry surface after curing protective coating fast curing fluorescing blue |
Vitralit® 9179 | 200-400 | acrylate | UV |
Fast curing very well suited for automated production lines yellow color dry surface |
Vitralit® 90008 | ||||
Vitralit® 90013 | 900-1,500 | acrylate |
UV VIS |
excellent adhesion to polyimide films high ionic purity high flexibility highly resistant to moisture and yellowing |
Vitralit® 90015 | 250-500 | acrylate |
UV VIS |
adheres to a variety of substrates including metal, ceramic, glass, epoxy board, and many plastics High ionic purity Extremely flexible Demonstrates excellent performance through thermal cycling |
Vitralit® 90086 | 500-800 | acrylate |
UV VIS |
Adheres to a variety of substrates including metal, ceramic, glass and many plastics Extremely flexible Excellent optical clarity Outstanding elongation and memory Tack-free surface |
Vitralit® 90830 | 900-1,500 | acrylate |
UV VIS |
Adheres to many low surface energy plastics including PE, PET, polyester as well as many other polymer blends Self-levelling Extremely flexible Excellent performance through thermal cycling |
Structalit® 5521 | 1,200-2,000 (Rheometer, 25°C, 10s^-1) | epoxy | thermal at 60°C |
Non-conductive Outstanding adhesion to high performance plastics (LCP, PBT) High purity Electronic grade standard Flexible |
Structalit® 5531 | 5,000-10,000 (Rheometer, 25°C, 10s^-1) | epoxy | thermal at 60°C |
Non-conductive Outstanding adhesion to high performance plastics (LCP, PBT) High purity Electronic grade standard Good mechanical stability Good chemical resistance |
Structalit® 8801 T | 16,000-30,000 (Rheometer, 25 °C, 5s^-1) | epoxy | thermal |
Resistant to oils, grease and fuels; Stable; Fast curing at low temperatures |
*UV = 320 - 390 nm VIS = 405 nm
To download the technical datasheets (TDS) please click on the adhesive name.