UV Masking Materials for Metal Finishing Processes
Metal finishing operations often incorporate removable protective barriers or temporary masks to protect component surfaces and cavities during processing. For years, temperature resistant tapes, waxes, and solvent or water-based coatings were the only protective masks available for processes such as grit blasting, shot peening, acid stripping, and plating. Applying these masks is very labor intensive and lengthy process. Performance is not always consistent, which can lead to substantial cost overruns from rework and scrap.
An alternative to traditional masking materials and methods is available from Panacol-USA. Highly resilient masking materials that cure in seconds with UV/visible light are offered for the specific purpose of temporary surface protection. These UV Masking materials can be easily dispensed on surfaces and into cavities by manual methods or through automated dispensing systems. Once dispensed, the liquid UV Mask is cured (hardened) in seconds using a UV light source. These light sources can be traditional broad spectrum discharge lamps, or new generation high efficiency LED systems. This technology can dramatically reduce labor costs and cycle time.
Each Panacol UV Mask will have one or more options for removal. All can be removed by incineration (900°F to 1200°F). Quite often, the incineration process can be combined with an existing component heat treating operation for maximum process efficiency. Component surfaces are residue-free after the masks are removed, and ready for the next operation. The highest adhesion UV Masks are ideal for hot engine or turbine components subjected to processes that include grinding, machining, acid strip, plasma spray, and HVOF.
Many Panacol UV Masks can be removed by peel. Lower adhesion masks formulated for mild grit blast, shot peening, and paint may be peeled at room temperature. For processes that include plating, anodizing, vibratory tumbling, and high-impact blasting, high adhesion UV Masks are required. The peel process requires a short, hot water soak to make the cured UV mask more pliable for peeling. Dry heat may also be used for this purpose.
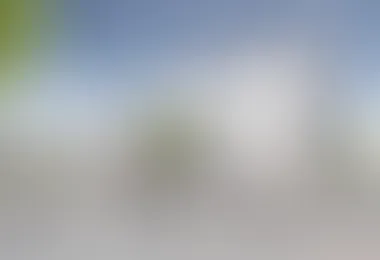
Panacol UV masking material provides surface protection during grit blasting
UV Curing Equipment:
UV system solutions with Panacol UV Masks and innovative curing systems from Honle
Download Brochure:
A limited number of Panacol UV Masks can be removed using a water bath with agitation or ultrasonics. These water soluble masks dissolve when immersed in water. Agitation accelerates the removal process. Water soluble masks are best suited for smaller components being subjected to etching, light grinding, polishing, or the application of coatings.
In addition to the surface finishing of components, Panacol UV Masks can be used as processing aids for the functional testing of components. Air flow testing requires the temporary blocking of certain hole patterns. Panacol UV masks may be used to quickly seal the necessary holes or channels for testing, and then be removed as required. Internal cavities may also be filled with Panacol’s thermal curing UV Masks to provide protection from accidental back strikes when laser drilling holes.
Panacol UV Masking Materials can ensure that high value components are better protected from handling damage during transportation. Highly polished surfaces, tight tolerance bores, or fine threads can be coated and encased with peelable UV Masks.
As an added benefit, Panacol UV Masking Materials can extend the life of fixtures that are used to secure components during machining, blasting, peening, and plating operations. After showing signs of wear, the UV mask can be removed and replaced, preserving the surfaces of the fixture beneath the UV masking material.
Please download our brochure or open one of the product links below to view our selection of UV Masking Materials. Or, contact Panacol-USA Applications Engineering to speak with a masking specialist who can guide you to a product best suited for your application.
Masking Material | Viscosity [mPas] | Base | Properties | Removal Method |
---|---|---|---|---|
Vitralit® MASK 20100 | 200-400 | acrylate | Moderate adhesion, water soluble mask, dissolves in hot water | Dissolve in hot agitated water |
Vitralit® MASK 20101 | 10,000-40,000 | acrylate | Hard, very high adhesion, acid resistant |
Incinerate @ 900°F or higher (approx. 500°C) |
Vitralit® MASK E-20102-G | 8,000-15,000 (Rheometer, 25 °C, 10s^-1) | acrylate |
Green color, high adhesion, durable |
Peel after hot water soak (2-3 minutes @ mininmum 176°F/80°C) |
Vitralit® MASK 20102-G-Gel | 50,000-70,000 | acrylate |
High viscosity, green color, thixotropic gel version of Vitralit MASK 20102-G |
Peel after hot water soak (2-3 minutes @ minimum 150°F/65°C) |
Vitralit® MASK 20104 | 14,000-17,000 | acrylate | Translucent, moderate adhesion | Peel @ room temperature |
Vitralit® MASK 20107 | 40,000-60,000 | acrylate | Moderate adhesion | Peel after hot water soak, 2-3 minutes @min. 122°F/50°C |
Vitralit® MASK 20109 | 15,000-40,000 | acrylate | Low adhesion | Peel @ room temperature |
Vitralit® MASK 20110 | 50,000-70,000 | acrylate | Very thick, low adhesion | Peel @ room temperature |
Vitralit® MASK 20111 | 30,000-50,000 | acrylate |
Mask for protective coatings, wave solder, white color |
Peel @ room temperature |
Vitralit® MASK 20114 | 90-150 | acrylate | Low viscosity cavity fill |
Incinerate @ 900°F or higher (approx. 500°C) |
Vitralit® MASK 20115 | thixotropic | acrylate |
Controlled flow properties, extremely clean burn-off |
Incinerate @ 900°F or higher (approx. 500°C) |
Vitralit® MASK 20116 | 50,000-70,000 | acrylate | High viscosity cavity fill |
Incinerate @ 900°F or higher (approx. 500°C) |
Vitralit® MASK 20117 | 20,000-30,000 | acrylate |
Very high adhesion, peelable mask, green color |
Peel after hot water soak (2-3 minutes @ minimum 150°F/65°C) |
To download the technical datasheets (TDS) please click on the adhesive name.